Kindling Collector: Wood-chopping tool project
Kindling Collector hired Pro-Dev to design, engineer and manufacture their new startup product - The Kindling Collector that contains the firewood/kindling while being split. The product improves both safety and convenience.
The project began with a comprehensive discussion on the design requirements and the direction to take. We decided it needed to be robust, deflect axe blows where possible, have a purposeful but attractive style, and be cost effective both to tool up and produce.
The next step was to define the scope of the project in a detailed 3-page document that spelled out the form, function, cost and compliance requirements. The scope document made a good starting point but constantly evolved throughout the project.
We then broke down the overall project into manageable chunks and started the initial design work (conceptual stage). During this stage we designed sketches and CAD concepts to present to the client and seek feedback. We did this for a number of iterations, eventually settling on what the client needed and was happy with.
The next step to was detail the parts and assemblies to make a physical prototype to present to the client. Once the direction was confirmed, a set of steel factory build prototypes were made that the customer was able to test thoroughly and begin to obtain crowd funding for production. This enables us to detail the CAD and create 2D drawings which can be used in the manufacturing process. Releasing parts for tooling/manufacturing is the most critical step in a project such as this because large investments are involved and care needs to be taken.
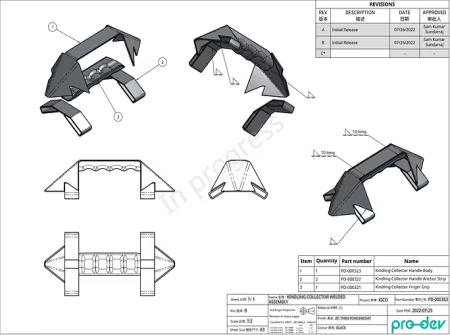
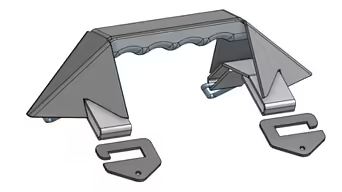
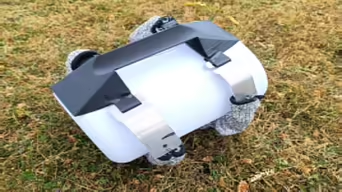
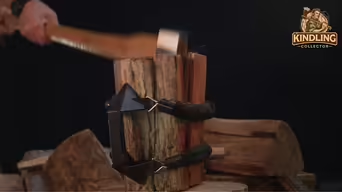
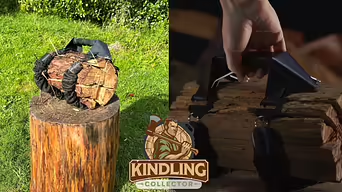
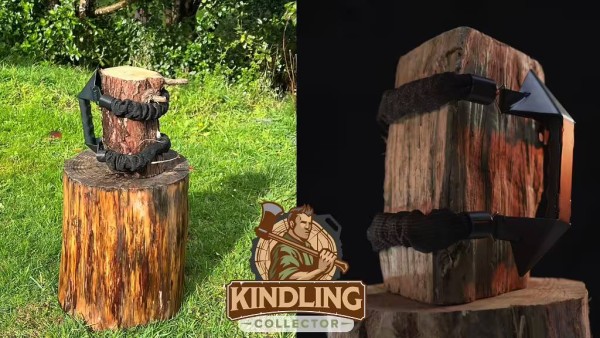
The above images show the sketch and concept CAD, the CAD 3D drawing, the 3D printed prototypes of individual parts, the complete product and the 2D CAD drawing.
When making the complete product prototype (shown above), we used our workshop skills to machine the many 3D printed and handmade parts needed. All the 3D printed or handmade parts were manufactured in our studio workshop. We used plastic, metal, and other materials to create a looks-like prototype, including some works-like features.
When we presented these life-sized full product prototypes to the client it gave them an opportunity to review it and gain a feel for the functions. This all occurred for a very small outlay and without any large amount of tooling or manufacturing. This is one of the major specialties of Pro-Dev – providing this kind of R&D product development service at a very affordable cost.
Once the client was happy with the prototype’s form and function, we moved on to factory build samples. We used Pro-Dev’s network of factories to create samples identical to the items the client will receive once in production.
We have been working closely with all the factories involved to ensure the highest quality standard. This project demonstrated Pro-Dev’s full suite of services and how a potential client can best use us. Clients can work with us up to CAD stage, to prototype stage or use our full range of services up to and including packaging and manufacturing.